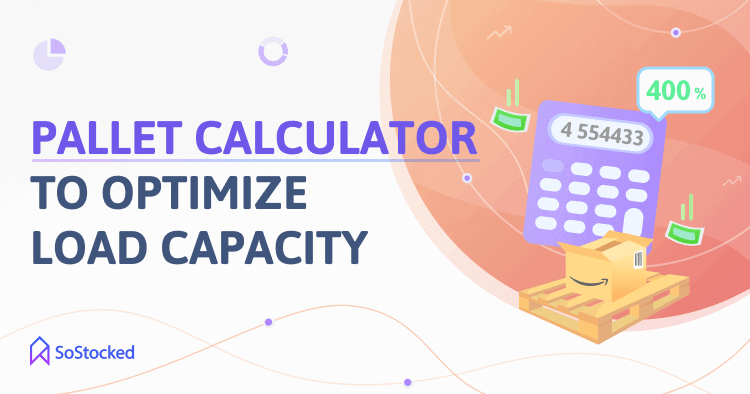
How to Use a Pallet Calculator to Optimize Your Pallet Load Capacity
Reduce Pallet Costs Through Smart Pallet Optimization
Pallet costs were reportedly up 400% compared to before the pandemic. The uptick in demand amid squeezed lumber supply and other supply chain concerns (port congestion, lack of containers, and trucker shortage) contributed greatly to the price surge. As a result, many businesses found themselves paying hundreds of dollars more for pallets, creating profit margin erosion that must be addressed immediately.
With pallet costs approaching record highs, it’s time to look at pallet optimization as a way to reduce your overall shipping costs. It can also help lower storage costs because storage is done per pallet. Optimizing pallet load capacity reduces the total number of pallets, and thus reduces your per pallet storage cost.
Pallet optimization is the planning and building of a pallet to ensure best use of its available space, i.e., to get as many units per pallet as possible. By being able to store & ship more units at once, you can save a lot of money on freight & storage costs and other expenses.
For example, if your carton is 25 inches long and you have a pallet that’s 48 inches long, you can only fit one carton across that pallet length. But if it’s 24 inches, you can fit 2 cartons across that pallet length. This is a huge difference in what is possible in terms of getting the maximum units per pallet.
However, carton and pallet dimensions are just two of the many other factors you need to look at when it comes to pallet optimization. You also need to factor in unit dimensions, pallet layers, pallet load height, and maximum allowable pallet weight, among other essential variables. This will help you to truly figure out the best way to put your units into the cartons and your cartons onto the pallets.
Sounds like a lot of work? Don’t fret. This is where well-thought-out pallet calculators come in handy.
Read on to learn more about pallets and why they’re important. I’m also going to share some tips on how to choose the right pallet for your business, how to use a pallet calculator, and more importantly how to reduce pallet costs.
In this Pallet Calculator guide, we’ll take a look at:
What is a Pallet?
A pallet is a portable platform that serves as a sturdy base for your inventory. It is mainly used for storing, stacking, handling, and transporting goods. Pallets are also designed to be lifted by material handling equipment like forklifts and pallet jacks.
While most types of pallets look the same, they aren’t built out of the same materials. Pallets typically vary by material (wood, metal, plastic, and paper), structural design, and entry point to suit different product loads and requirements.
Pallet Types by Structural Design
Block Pallets
As the name suggests, block pallets are known for the blocks (of wood) that form its base. One pallet typically consists of nine blocks, each placed in each corner, in the center of each side of the pallet, and right in the middle of the pallet itself to provide excellent structural support. Block pallets are also known as four-way access pallets because forklifts and pallet jacks can access them from all sides. They can also be built with or without bottom deckboards.
Stringer Pallets
In contrast to block pallets, stringer pallets use 2 x 4’s or 3 x 4’s (lumber) instead of blocks to support the unit load. Stringers are placed between the top and bottom deckboards.
Stringer pallets are generally designed to have two entry points, which means they can only be accessed from two sides.
Pallet Types by Entry Point
2-way access pallets
This pallet type has access points on two sides (front and rear) for the forklift’s forks.
4-way access pallets
These pallets have entry points on all four sides, so they can be accessed from any side using a forklift or a pallet jack.
Open-deck pallets
This type of pallet has spaces between the deckboards (a flat surface for cartons to rest on), making it more lightweight than other pallets. However, it’s not ideal for shipping smaller items because they will slip through the gaps.
Solid deck pallets
These pallets only have a single large top deckboard without any gaps in between, making them perfect for small items versus open-deck pallets.
Double-face pallets
Compared to solid decks, double-face pallets have a top deck and a bottom deck for enhanced structural strength. The decks can either be open-boarded (with gaps) or close-boarded (without gaps).
Pro tip: Certain industries have specific requirements for pallets, so you should refer to the laws, regulations and standards for your specific industry to learn more about what type of pallet is appropriate for use in your business. If you’re an Amazon seller, continue reading to learn more about Amazon’s pallet requirements.
Why Are Pallets Important?
Pallets are important because they help:
Protect Goods in Overland, Air, or Sea Transit
Many sellers don’t use pallets in shipping containers and floor-load (the cartons are loaded into the floor of the container rather than putting them on pallets) instead to maximize space. However, more recently, some sellers have been palletizing to avoid breakage as the ports have been chaotic. For this reason, the packing of containers has also not been as professionally done as it used to be. This means lots of excess shifting and crushing of boxes. So, pallets can be used to protect goods in transit.
Pro tip: If you’re planning to use pallets within your shipping containers, keep in mind that a 20-foot container can typically hold 9 to 10 40×48-inch pallets in one tier, while a 40-foot container can hold 20-21 of the same pallet size in one tier. This setup allows ample clearance between the pallets and the container walls, roof, and door so that forklift operators can safely and efficiently move your pallets.
Speed up Loading and Unloading Time
Rather than loading or unloading individual cartons or units, pallets allow you to move items in bulk easily. Simply put your boxes on a pallet, shrink wrap them, and you can move multiple cartons at once.
Keep Warehouse Costs Down and Enhance Logistics
If you have your own warehouses, faster loading and unloading times will help reduce labor costs because there’s less need for your staff to work overtime.
Ensure Good Working Conditions and Employee Safety
Moving multiple boxes on a pallet is a lot more stable (and safer) than loosely stacked items that can fall off of the pallet when you’re turning a corner, for example. You might argue that a poorly loaded pallet can also present some risk, but training your employees to load/unload pallets safely can help decrease the chance of work-related injuries.
Related: 3PL Logistics Backup for Amazon
How to Choose the Best Pallet for Your Business
Choose the correct pallet type to avoid repalletization at your 3PL warehouse, which comes at an added cost, or worse, get penalized by Amazon for having the wrong pallet type.
Here are the top six things you should consider before investing in pallets.
Amazon Pallet Requirements
Before shipping your inventory to Amazon, make sure that your pallets meet the following requirements:
Pallet Type
Ship your products on 40 x 48-inch, 4-way access wooden pallets.
Grocery Manufacturers Association (GMA) Pallet Specifications
The food industry, including Amazon, follows the pallet guidelines set by the Grocery Manufacturers Association (GMA)–recently rebranded as the Consumer Brands Association. These guidelines aim to ensure fast and smooth movement of products throughout the US.
Based on GMA’s guidelines, pallets are divided into two main groups – Grade A and Grade B – to identify the differences between the most like-new pallets and those with minor cracks or imperfections. In some cases, these grades are also referred to as #1 and #2. These grades are based on the pallet’s general appearance (Grade B pallets normally have a more worn appearance than Grade A pallets), compliance with GMA requirements, structural integrity, and how much repair is needed to make the pallet usable.
Within Grades A and B, there are several subcategories to make a clearer distinction between higher quality and lower quality pallets. It’s best to familiarize yourself with these classifications to better understand Amazon’s pallet requirements, so you can request the correct pallets from your suppliers or freight forwarders.
Premium Grade A or #1A
Often marketed as good as new, premium Grade A pallets have a bright wooden color and have no visible signs of extensive repair. Not only are they perfect for shipping and storing food and grocery items, but also for in-store visual merchandising (improving your product’s visual presentation to better highlight their features and benefits). Some grocery stores use premium pallets as part of their retail display to attract the attention of shoppers.
Melon Grade or #1B
These pallets are almost similar to #1A, in that they normally don’t have any obvious signs of repair. The only difference is that Melon Grades often have some minor damage or discoloration, making them slightly inferior to their premium Grade A counterparts.
Regular Grade A or 1R
Sometimes referred to as Regular Grade, these pallets have been refurbished to achieve like-new condition–for example, replacing damaged or broken deckboards with good-quality recycled boards to match the pallet being repaired. This makes 1R pallets more affordable than Premium A and Melon grades, although they generally have a more worn appearance.
Premium Grade B or #2
These pallets may have had some type of repair done to one of the stringers. For example, adding a sturdy piece of wood to the broken or cracked stringer for extra support. However, these repairs should make the premium B grades durable and stable enough to carry loads without trouble.
Standard Grade B
This grade is the lowest standard grade offered by many manufacturers. This also means B grades are the cheapest, albeit some parts of these pallets may either be cracked or missing, thus they will likely need to undergo extensive repair versus higher grades that are still fairly in good shape save for a few discolorations or minor repairs.
To stay compliant with Amazon’s pallet requirements, be sure to follow the guidelines below:
Ship units on GMA Standard B Grade or higher pallets that have:
- 6 or 7 top deckboards. The amount of top deckboards will largely depend on the width of the boards.
- 4 access points
- At least 4 bottom deckboards
- 3 stringers
- No obvious signs of repair done to the stringers (e.g., reinforcing the stringers with a wooden block or a metal plate)
Ship grocery items on GMA 1A Grade pallets that have:
- 7 top deckboards
- 5 bottom deckboards
- 4 access points
- 3 stringers
- No block repairs done to the stringers
Ship health and personal products on GMA 1A and 1B Grade pallets that have:
- 6 or 7 top deckboards. Again, the amount of top boards you can attach to your pallet depends on board thickness.
- At least 4 bottom deckboards
- 4 access points
- 3 stringers
- Only one stringer may have some type of repair. For example, adding a block or plug (a piece of a stringer nailed next to an existing damaged stringer) to improve the overall structural integrity of the pallet.
Lastly, only use pallets in good condition. Damaged or broken pallets may be rejected by Amazon at your expense.
Pallet Height
AMZ maximum allowable height for pallets depend mainly on whether you’re using a:
Non-Stackable Pallet
Also known as single pallet, a non-stackable pallet is a pallet that cannot be stacked due to the odd shape of the unit it’s holding or simply because it has a “Do Not Stack” label affixed to it. A single pallet freight shipment must not exceed 72 inches in order to be approved by Amazon.
Keep in mind that you will also have to take the height of the pallet itself into these limitations. A standard 40 x 48 inches pallet normally has a height of 6 inches. That means you only have 66 inches (72 – 6) of carton height to stack if using a non-stackable pallet.
Note that some carriers like FedEx apply a surcharge to non-stackable freight shipments. This is generally due to the fact that a non-stackable 72” pallet takes up less vertical space in the truck than a pair of stackables does. Carriers, therefore, may want to charge you for the unused space. Check with your carrier for more details.
Stackable Pallet
Stackable pallet means stacking two or more pallets on top of each other. You can ship your units on a double-stacked pallet into Amazon, but the total stacking height, including the pallets, must not be higher than 100 inches (50 inches per pallet stack). So, for each stackable pallet, you only have 44 inches of carton stack height due to the 6” of pallet materials. Using a double-stacked pallet is space-efficient as it allows you to maximize vertical trailer space for standard semi-trailer height. So, it can be a good option if you regularly send in hundreds of boxes per Less than Truckload (LTL) or Full Truckload (FTL) delivery.
Pro tip: Talk with your 3PL to find out what they prefer (stackable or non-stackable). It’s important to consider the height of your truck when palletizing, as you may be able to fit more units per truckload with a pair of stackable pallets than a single pallet. But again, discuss with your 3PL for the best advice. Additionally, read Amazon’s Seller Requirements for LTL, FTL, and FCL Deliveries for more information.
Floor Loading
If you’re thinking about floor loading your shipments to maximize space and reduce costs (no need to buy pallets), bear in mind that floor loading does not work for all shipments.
Heavy and bulky items, such as carpets, large appliances, furniture, cast iron pipes, or tires may arrive in floor-loaded containers. But fragile goods shouldn’t be floor loaded to reduce risk of damage during transport.
In addition, Amazon often rejects floor-loaded shipments that require extensive warehouse labor or handling, such as boxes that weigh more than 50lbs each. Or, those shipped in a trailer with a corrugated or uneven floor.
And since floor-loaded shipments require extra work, it takes longer for warehouse associates to process your inventory, which may delay its availability for sale on Amazon. That’s why Amazon recommends palletizing your inventory as much as possible to avoid such costly delays.
But if palletizing isn’t really an option for you right now, make sure to notify your carrier when you know that your shipment will be floor loaded. They will then review your request and let you know whether your floor-loaded shipment is accepted. If accepted, they may impose extra charges that would vary depending on the extra handling and time required to process your cargo.
When preparing your floor-loaded shipment, work closely with your carrier to make sure your shipment meets Amazon’s Floor Loading Policy. This will help you to avoid unnecessary charges or shipment rejections and to ensure safe loading/unloading procedures and timely delivery and check-in.
Pallet Weight
The total weight of the pallet – both stackable and non-stackable – must not go over 1,500lbs (680kgs). To ensure efficient loading/unloading, receipt, and storage of your products in FBA, each carton on the pallet should not weigh more than Amazon’s standard box weight limit of 50lbs (23kgs), unless it contains a single large or oversize unit that weighs more than 50lbs.
Pallet’s Compatibility with Your 3PL’s Current Handling Equipment
Pallets are usually categorized as two-way and four-way, and each has effects on how they can be lifted or handled. For example, forklifts can’t enter a two-way pallet through the sides of the stringers (i.e., it can only be lifted from the front and back), whereas four-way entry pallets can be accessed from any side. This is something very crucial for some warehouses. In fact, certain warehouses like Amazon only utilize four-way access pallets mainly because they’re more efficient and convenient than pallets with only two entry points.
So, make sure that your pallets work with your 3PL’s existing handling equipment before making that investment. Again, talk to your 3PL if you have any concerns.
Load Capacity
Load capacity refers to the maximum weight a pallet can hold. Make sure that your pallets can handle the load you expect them to carry.
Remember that Amazon has set a total weight limit of 1,500lbs per pallet. So, if your cargo weight is going to be that heavy, use pallets that are made out of sturdy and high-quality materials.
For instance, hardwood (oak and pine) is ideal for shipping heavy items. Conversely, lightweight wooden pallets (plywood) or those that have been badly damaged due to extensive use might not be durable enough to hold your inventory once fully loaded.
Durability
Durability refers to the ability of the pallet to withstand the impact of rough handling as it goes through various stages of shipping (e.g., moved along by forklift or conveyor). When testing for durability, look for signs of wear and tear on the pallet, such as the impact of forklift blades (aka fork tines) on the deckboards. If the damage is extensive, you may need to replace them with new ones or higher-grade pallets.
If the pallet is for single use only, then durability may not be a crucial factor in your decision. Volume or cargo weight is also another thing to consider when making a selection. If you’re planning to ship high volumes or heavy objects across long distances, you will need to use premium pallets to get the best value for your hard-earned money.
Pallet Stiffness
Pallet stiffness can be defined as the measure of how much a pallet bends out of shape under load over time. If the pallet collapses, boxes will bulge at the sides due to crushing pressure, resulting in load instability and damage to your products.
It’s crucial that the pallets will hold their shape when fully loaded. The heavier your cargo is, the higher stiffness rating you’ll need to transport the units within the boxes safely.
When it comes to wooden pallet stiffness, thicker deck boards are always better. While thicker pallets are more expensive than thinner pallets, the benefits simply outweigh the risks, including the cost of inventory shrinkage due to damage.
Pro tip: Investing in stiffer pallets is just one way to ensure maximum protection of your cargo. Using sturdy boxes is just as important. The compression strength of boxes (ability to withstand pressure when placed between upper and lower boxes) can be increased by adjusting the flute size and cardboard grade. Check out How to Choose the Right Master Carton Size and Type for more information.
Budget
How much are you willing to shell out for pallets? Which pallet type will provide the best value?
Price may be a huge factor in your selection process, especially given the fact that, as of November 2021, it would now cost you around $21 to buy a new wooden pallet in the US. Before the pandemic, pallets only cost $12 a piece. A $9 increase over the last 12 months (2020 to 2021) is huge for many sellers, and therefore, buying pallets at today’s price understandably requires some serious consideration.
However, you still can’t go wrong with high-quality pallets as they are less likely to break down at your warehouse, while in transit, or at Amazon. Anything less could lead to inventory breakage and additional fees for new pallets and repalletizing, costing you more money in the end.
Pallet Calculator: How Many Boxes Will Fit on a Pallet?
Box count per pallet may vary depending on your box sizes. You can use a pallet calculator to accurately determine your optimal pallet load capacity. Arming yourself with this kind of information will help you make more informed decisions about your:
Product packaging
If it’s too tall or too large, perhaps shave off a couple of inches to achieve the smallest dimensions possible. This strategy will allow you to fit more units per carton and per pallet. It may also help you get into the lower shipping fee tier with major carriers and reduce your fulfillment and storage costs with Amazon. Overall, run your calculations and see if you can adjust anything so you’ll be paying less in shipping and storage fees.
Related: New Dimensional Weight Fees Placing Further Strain on Profit Margins
Carton type and size
Consider right-sizing your cartons (using only what’s necessary, i.e., little or no bubble wrap or foam fillers or replacing heavy packaging materials with lighter ones) to be able to fit as many units per carton as possible. Read my blog post, Master Carton Calculator, to take a deep dive into master carton optimization.
Pallet configuration
This refers to four things: pallet type and size, stacking pattern (block, brick, or pinwheel), your product packaging (boxes or bags), and the number of cartons stored per layer and per pallet. Depending on your type of product packaging or carton size, you may be able to fit two or more items per row/layer. Choosing the correct pallet type (stackable or non-stackable) and stacking pattern for your shipment can be key to maximizing your pallet’s volume usage.
Put simply, pallet optimization means making the most of your pallet’s usable space. And a smart pallet calculator should be able to help you figure out how to achieve that.
However, of all the pallet calculators that I have come across, I have found that none of them are diving into all of the calculations fully because they don’t include other variables relevant to Amazon sellers. Remember my tip above about how you also need to look at the unit, carton and pallet dimensions altogether to determine the correct carton size to maximize pallet space.
No one has been doing this exactly right regarding pallet calculators, so we built our own calculator. It basically lets you factor in all those variables I’ve mentioned and Amazon’s pallet guidelines to give you the most accurate calculations possible.
See for yourself: Master Carton and Pallet Calculator
4 Top Tips to Lower Pallet Costs
The most effective way to lower pallet costs is by following the best pallet optimization techniques. These include:
Run Your Calculations and Make the Necessary Adjustments
With shipping costs expected to keep rising in 2022, you want to make sure you get as close to 100% pallet volume usage percentage to save money.
Getting as many units or cartons per pallet allows you to reduce the total number of pallets you need.
If you can get 150 units per pallet instead of 100, a 6,000-unit order takes only 40 pallets instead of 60. That can give you $420 worth of savings based on today’s pallet rates.
Wooden pallet cost:
- $21 per piece
- 40 x $21 = $840
- 60 x $21 = $1260
- $1260 – $840 = $420
Optimize Your Product Packaging
Smart packaging optimization can also help you save on FBA fulfillment and storage fees. Remember, Amazon charges per cubic foot. So, by reducing your product packaging, it can help you get into a lower product size tier, which means lower storage and fulfillment fees. Plus, even slight packaging adjustments like eliminating excess air from your packaging (e.g., cereal packs) can make your product smaller and lighter, which can also help reduce carbon footprint.
Related: Is Amazon Climate Pledge Certification Worth It For Sellers?
Optimizing your product packaging (and cartons) can also lead to increased warehouse shelving capacity at 3PLs that charge per pallet. With improved warehouse shelving capacity, you will be able to fit (and sell) more units per pallet without increasing your storage space, allowing you to save on storage costs and maintain profitability.
Here’s an example.
If a pallet costs $40/month to store and you can get 1,600 units on that pallet via pallet optimization, that would only cost you $0.025 per unit versus 960 units (without optimization), which would cost you $0.042 per unit. That’s $0.017 more per unit.
If you’re selling 100,000 units a year, that’s $1,700 in additional pallet cost savings. Extend that across your entire catalog of FBA products and you could be looking at thousands in savings with just pallet optimization alone.
Again, run multiple scenarios using a pallet calculator to figure out the best way to optimize your pallet load capacity.
Pro tip: Amazon inventory restrictions still apply, so keep your restock limits in mind when creating a shipping plan. Our calculator offers the option to plug in your daily sales velocity in order to restrict master carton size to a maximum of only two months worth of inventory to restrict you from sending in too much inventory for extremely slow sellers.
Related: 2021 Amazon Restock Limits Tips and Updates
Choose the Right Stacking Pattern for Your Inventory
Once you figure out how many cartons will fit on your pallet, the next step is to determine the most efficient way to stack them to ensure proper load and weight distribution.
There are three types of pallet pattern styles that carriers recommend shippers should follow.
Block or Column Stack
Cartons are stacked directly on top of each other, which allows for maximum stacking strength. This means you might not need to invest in more premium cartons so you can keep your costs down.
Pinwheel Stack
This stacking pattern typically consists of four boxes or bags placed perpendicular to one another to create a pinwheel and to lock everything in place.
Brick or Interlocking Stack
A brick stack pattern involves alternating the way boxes are stacked so that each row is offset, creating a pattern similar to a brick wall. An interlocking pattern provides excellent resistance against lateral motion and keeps loads from shifting. It also usually works best if you are stacking cartons of the same size.
The orientation of cartons in your palletized shipments can have a huge impact on the integrity of your products. If you want to keep costs low, it’s crucial to avoid inventory shrinkage from damage as much as possible.
I recommend discussing stacking patterns with your 3PL to help you make the right choice for your product and packaging. For example, block and brick patterns are often used with master cartons, cubed boxes, or packaging materials with even surfaces, while pinwheel stacking is often used for bags (e.g., dry dog food, sacks of rice, bags of cement, and sandbags).
Stacking patterns that carriers don’t recommend are:
- Overhanging. Certain parts of the cartons are hanging over the edge of the pallet.
- Pyramid stacking. Putting smaller or lighter boxes at the top of the pallet, which causes the stack to get narrow as it gets higher.
Overhanging can reduce box compression strength by around 32%, according to FedEx. And pyramid stacking does not provide an even surface for your cartons, so those at the top are at risk of getting damaged from other shipments near or above them.
Whatever pallet pattern style you end up selecting, see to it that it’s as cubic as possible. This shape is simply more stable and efficient.
Don’t Allow For Any Wide Gaps In-Between Cartons
Take a look at the footprint of your cases or bags on the pallet. Are there any wide gaps? Could one or more cartons be squeezed in somewhere?
Work out a good pallet footprint with your 3PL that will eliminate any unnecessary wide gaps between your cartons. You’ll be surprised to find that changing your pallet footprint can sometimes allow you to squeeze in one more carton or pack per layer, thereby increasing the total number of units you can load per pallet. This also means you may be able to ship and store more units for the same transport and storage cost.
Related: How to Ship to Amazon FBA and Speed Up Check In Times
Use SoStocked to Track Your Inventory
Ready to ship your inventory to Amazon? Make sure to enable inventory tracking by using the following software tools and features:
Purchase Order (PO) System with Lead Times
Enhance your inventory order and transfer (warehouse to FBA) processes with an advanced system that allows you to create and send purchase orders online. You can also assign lead times to each of your purchase orders so you can easily track your on-order inventory each step of the way: from in production to en-route to arrival at your warehouse or FBA.
Our PO system also works hand-in-hand with our Work Orders (WO), a secondary order management system that lets you create a set of instructions for prep work to be done on your existing inventory. That work may be to:
Order Tracker
- Transfer your inventory from 3PL to FBA
- Bundle multiple units into a single sellable pack
- Store your inventory
- Prep your inventory for commingling, i.e., skip the labeling process
- Repalletize your shipments to ensure Amazon compliance
Keep a firm eye on the movement of your inventory orders, from in production > shipping > customs > arrival at the final destination. You can track everything from a neat Kanban board that automatically updates the progress of your shipments based on your assigned lead times.
Inventory Tracking Dashboards
Use our Inventory Tracking dashboards to track in-transit shipments and monitor inventory on-hand levels at your 3PL warehouse and Amazon fulfillment centers.
Go to the Inbound Shipments dashboard to view POs/WOs that are in production or en route. This also tells you where your inbound inventory is going (3PL, prep center, or FBA).
In addition, use Inventory On-Hand Dashboards to track your on-hand inventory, including reserved inventory, across all Amazon marketplaces (US, Mexico, UK, etc.) and warehouses.
Split a Shipment
Split a shipment within the same purchase order if you need to ship half of your order by air and another half by sea. You can also use this tool if you’re shipping a portion to your 3PL warehouse and the rest directly to Amazon.
Bonus: Join my free live webinar to learn How Flexibility and Optimization can Recover Your Margins
Optimize Your Pallets to Stay Profitable Amid Rising Shipping Costs
All in all, pallet optimization can be an effective way to protect your profit margins against surging shipping costs.
If you have to spend $100 on pallets per month and tens of thousands more on sea and ground freight, then you might as well make sure you get as many units on each pallet as possible and as many units in your LTL/FTL shipments as possible to get your money’s worth.
But for that to happen, it is best to start by paying closer attention to your product size and packaging materials. Does your packaging need to be that bulky? Is there anything you can do to cut the size down to a lower tier (from small oversize to large standard size)? Or, perhaps replace hefty packaging materials with lighter, recyclable ones to make your cartons compact and eco-friendly?
Try to run multiple calculations using a pallet calculator to determine your optimal unit, carton, and pallet dimensions. Right-sizing your product packaging and cartons will allow you to fit more units per pallet.
Once you reach the palletizing stage, the next step is to figure out which pallet configuration to use. Make sure there are no unnecessary wide gaps between your cases to make the most of your pallet space. Lastly, keep an eye on your products using our inventory tracking tool and inventory dashboards to minimize shrinkage.
Need more information?
- Send Message: We typically reply within 2 hours during office hours.
- Schedule Demo: Dive deeper into the nuances of our software with Chelsea.
- Join Live Upcoming Webinar: New to Amazon inventory management? Learn three inventory techniques you can implement right away.