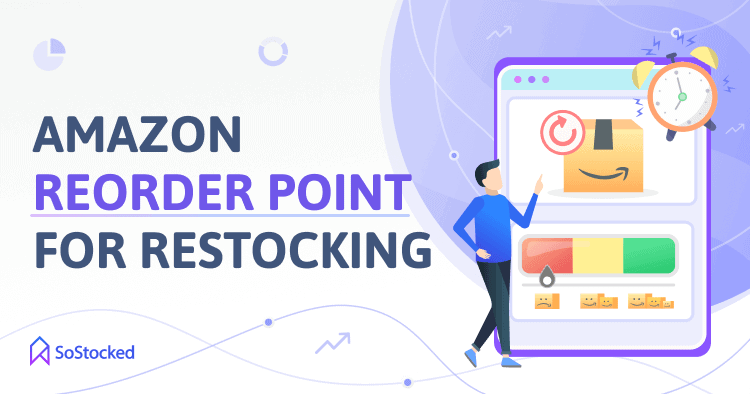
Amazon Reorder Point: How To Calculate For Restocking
ROP Calculation and Automation Tips
Poor restocking processes can have a detrimental effect on your inventory plans. When inventory shipments don’t arrive on time because you ordered too late and you don’t have a safety stock that acts as a cushion in cases like this, it increases your risk of stocking out. When they do come, but the demand has already passed, such as after a holiday or sales season, you’ll be stuck with hundreds of units that your customers no longer want.
Both scenarios can throw your plans into disarray. For example, you have to cancel an upcoming sales event because your inventory is too low for the event or you instead find yourself spending more cash to airship your inventory to arrive in time for the sale.
Either situation would lead to lost sales and additional holding costs or overspend on express shipping costs.
So how do you determine how much stock to order and when?
In this Amazon Reorder Point guide, we’ll take a look at:
What Is Amazon Reorder Point?
Reorder Point (ROP) is the stock level at which your inventory needs to be replenished. Once your stock reaches reorder point, it means you should place your next order immediately to avoid a potential stockout.
ROP is the buffer stock metric that tells you:
- The right time to order more stock from your supplier.
- Or, for suppliers, the right time to create a Manufacturing Order (MO) to make more products.
But those two things aren’t the only reasons why it is essential to calculate your ROP. Another reason is that it gets harder to keep your inventory levels within optimal range as you handle more SKUs so expert coordination on this point is vital.
Setting a reorder point and automating your reordering process can optimize your inventory and reduce the risk of stockouts and excess stock while keeping inventory costs low.
SoStocked lets you set reorder points so you can get a notification when you need to order more stock to maintain an optimal inventory level. The software also allows you to set Buffer Stock Minimums and Max Stock Quantities in Days based on velocity so that you can avoid over or under-ordering. Using this feature enables you systemize your reordering process based on the data coming in from Amazon and the parameters that you have set.
5 Benefits of Calculating ROP
Keep Abreast of Stock Quantities
Knowledge of stock quantities keeps your Amazon business operational. When your inventory level triggers a reorder, you can immediately create a new purchase order to avoid running out of stock.
Amazon stock levels can also help you identify any potential excess stock. Suppose you aim to replenish your inventory every month. But three weeks in, you still have three weeks’ worth of supply above your buffer stock level for a particular product, which means your stock level is nowhere near the reorder point. In that case, you’ve got a slow-moving product you need to start ramping up sales on quickly. If neglected, excess inventory leads to higher storage fees and lower Amazon IPI scores and storage limits.
Efficient Replenishment System
Calculating and automating your reorder point will help you create an efficient inventory restocking system. When you know your reorder point, it’s easier to determine what to order, in what quantity, and when. You can then automate this repetitive process through inventory management programs like SoStocked, which allows you to set your minimum and maximum stock (in days or units).
Increased efficiency makes administrative tasks like restocking faster and easier, so you can eventually pass them off to your virtual assistant or supply chain manager. This way, you can focus on other core business functions like marketing and scaling your Amazon business.
Pro tip: Manage your FBA business better and optimize profits with these 7 Amazon Inventory Tips!
Enhanced Forecasting Accuracy
A good forecasting demand platform should help to give you an idea of historical buying trends over a particular period for your products. It lets you know the items that are selling like hotcakes during a particular season and those that won’t. This valuable insight allows you to seize new and recurring opportunities and adjust your inventory to handle expected spikes in demand. For example, by eliminating slow-moving products, you can free up some storage space that you can use to store more hot sellers. That’s why it’s crucial to calculate ROP properly for each of your products and use the reorder point formula correctly to work to improve the accuracy of your forecast data.
Improved Stock Count Process
Doing a stock count will be much easier if you continually keep an eye on your inventory levels. By that, I mean all year round, not only during your stock count day(s). If mistakes were made several weeks before your stocktake, it’d be too difficult to tidy things up by the time you discover them. The trick is to keep track of your inventory levels at all times and to spot inventory discrepancies early. Rather than relying on your warehouses to keep track of your inventory levels for you, keep your own accurate inventory accounting that you can use to audit the inventory amounts that they relay to you. As soon as something does not match, investigate and resolve it.
Having this accurate and up-to-date inventory count will help to ensure that your reorder points are operating properly using correct inventory levels, as without them, your reorder point projections will be completely off, causing you to over or under order.
Lower costs
By optimizing your inventory levels, you can keep your storage fees low and prevent tying up too much cash in inventory.
How to Calculate Your Amazon Reorder Point
In this section, I will break down the reorder point formula and tell you how to calculate it correctly.
Reorder Point Formula
Lead Time Demand + Safety Stock = Reorder Point
You can use an online reorder point calculator for a quick and easy calculation or SoStocked’s built-in, per ASIN reorder point calculation.
2 Reorder Point Variables
As seen above, there are two inputs required to calculate ROP. These are as follows:
Demand During Lead Time
Demand refers to your average daily sales velocity, and lead time means the days it takes the supplier to produce an order and ship it to your final destination.
Let’s say your Amazon business sells gaming computers and accessories, and you have a supplier in China from whom you buy LED monitors. Suppose it takes them three days to get the materials to manufacture LED monitors and three more days to assemble 1,500 units. In that case, your LED monitor supplier’s lead time to produce 1,500 units is six days. Once produced, it then takes 15 days to ship to your destination warehouse for a total of 21 days lead time.
What does this 21-day lead time mean
If you need all 1,500 LED monitors shipped on 25th September, you should place your purchase order on or before 4th September.
Additionally, suppose you have multiple SKUs with different suppliers. In that case, you have to consider the lead time of each supplier and most likely calculate a separate reorder point for each SKU as well. Lead time also varies depending on your supplier’s location. For example, overseas suppliers tend to have a longer lead time versus domestic suppliers or in-house production facilities.
To find lead time demand, multiply your supplier lead time (in days) by your average daily sales velocity.
Lead Time Demand Formula
Supplier Lead Time x Average Daily Sales Velocity = Lead Time Demand
Safety Stock
Also known as buffer stock, safety stock is the extra inventory that’s set aside in your warehouse and/or Amazon’s FBA warehouse to anticipate unexpected shipment delays and sudden demand spikes.
What is the relationship between reorder point and safety stock?
Your replenishment level is like your first line of defense against a potential stock-out. Safety stock provides the last line of defense that ensures you stay in stock in the event of sudden spikes in demand and unexpected supply chain problems that lead to longer lead times.
Simply put, safety stock is the minimum stock required for you to stay operational amid sales spikes and supplier delays, while ROP is the level at which you should replenish your inventory.
How to calculate your safety stock level?
Follow the steps below:
- Multiply your maximum daily orders by maximum lead time. Max lead time refers to the days required in case of supplier delays.
- Multiply your average daily orders by average lead time.
- Subtract the result of Step #2 from the result of Step #1.
Safety Stock Level Formula
(Max daily orders x Max lead time) – (Average daily orders x Average lead time) = Safety stock level
It is important to note that you may or may not keep all of this buffer stock at FBA. You may need to split your buffer stock between FBA and your 3rd party warehouse. In that case, calculating a separate buffer stock for FBA would be fitting using the same calculation but including FBA check-in and 3rd party warehouse transfer delays instead of supplier delays.
Calculating Your Amazon Reorder Point
Now that you know the factors influencing ROPs, let’s go back to the reorder point formula.
Reorder Point Formula
Lead Time Demand (or Average Daily Sales Velocity x Lead Time) + Safety Stock = Reorder Point
Sample computation:
Following the LED monitor example, let’s say your store sells 50 units of LED monitors daily, and your supplier’s lead time is 2 days (for easy math). The safety stock for this inventory is set at 250 units. Your ROP would be:
Reorder Point
(50 x 2) + 250 = 350 units
This sum indicates that you must replenish your LED monitor inventory when the stock level goes down to 350 units. This way, you’ll have sufficient stock to cover any increase in demand during the time it takes your supplier to produce and ship your order.
Pro Tip: Be mindful of fluctuations in your daily sales and lead times – crucial factors that influence your ROP. These metrics may change depending on the demand during a given period. This is where inventory management software like SoStocked comes in handy. SoStocked pulls real-time data and can adjust your ROPs accordingly. You can also customize additional variables, such as Minimum Order Quantity (MOQ), Minimum Transfer Quantity (MTQ), Order Schedule, and Transfer Schedule to tweak your order forecasting so that it works the way you need it to. Click here to learn more!
How to Automate Your Amazon Reordering Processes
With SoStocked, you can automate your reordering system in two different ways:
Use our free Amazon inventory spreadsheet template
Our Amazon inventory spreadsheet template is ideal for stores with five or fewer SKUs with fairly modest sales velocity. If you’re carrying a large number of SKUs, I recommend automating your reordering processes with software (see #2).
This template works with both Excel and Google Sheet apps, and more importantly, it has the following features:
- Inventory planner
- Inventory calculator
- Sales spikes log
- Stock out log
- Reorder recommendations
With these features, you’ll be able to:
- Remove stock-outs and sales spikes from your forecast data
- Factor in Lightning Deals and additional sales growth such as with planned PPC campaigns
- Factor for seasonality
- Incorporate any incoming shipments and any inventory being held in your external warehouse
- Calculate the optimal order quantity for purchase orders or the total amount of stock needed to be transferred from your warehouse to FBA.
Here’s how the reorder recommendations feature works:
Once you’ve put all the data required to calculate your reorder quantity, the template will show you three results:
- Your remaining days of inventory
- Reorder and transfer dates
- Order quantities needed for reorder and transfer
Lastly, go to the Order Quantity column to see your order quantity, which is calculated based on many different factors, such as your sales velocity, seasonality, safety stock, inbound shipments, and Lightning Deals.
Check out the full tutorial here.
Implement the Min-Max Restocking System through SoStocked
Min-Max is a smart reordering method that some of the more advanced retailers use. It uses the following formula:
- The minimum value represents the reorder point
- The maximum value is the highest amount of stock you don’t want to go over
- Subtract Min from Max to get your ideal order quantity
When your stock reaches the minimum level, it triggers a reorder alert. You then have to replenish your inventory to its max level and then sell that stock through to the min level and repeat the cycle.
We’ve incorporated this concept into SoStocked to make it easier for you to calculate your optimal order quantities and establish the optimal order and transfer frequencies. This way, you’re less likely to order too much or too little stock in your future orders.
SoStocked also has a feature that allows you to set your min and max values in units or days. However, we recommend putting them “in Days” as your number of units may fluctuate depending on demand or season.
Book a demo call now!
Take The Guesswork Out Of Forecasting
Reorder point is an important metric that tells you the optimal amount of stock to order and when. With a simple formula, you can calculate your reorder point and use that data to enhance your stock replenishment system. This method also takes the guesswork out of your forecast data too, so you’ll have a more accurate prediction in the future. This means you can better plan for potential demand spikes and stockouts, as well as keep storage costs low and your bottom line happy.
Need more information?
- Send Message: We typically reply within 2 hours during office hours.
- Schedule Demo: Dive deeper into the nuances of our software with Chelsea.
- Join Live Upcoming Webinar: New to Amazon inventory management? Learn three inventory techniques you can implement right away.