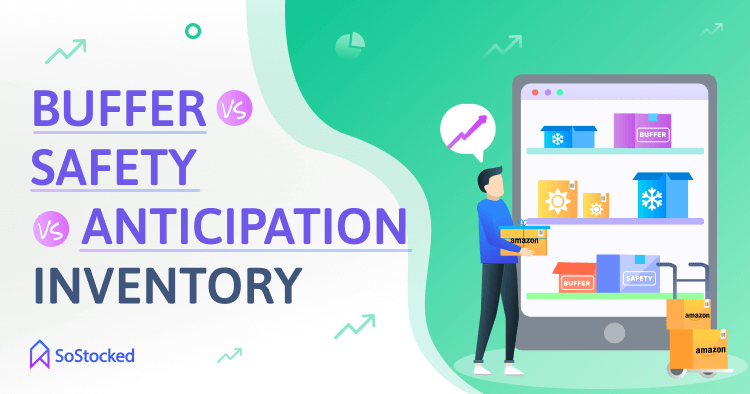
Buffer Stock vs Safety Stock vs Anticipation Inventory
What They Are & Why They’re Important
Planning out your inventory schedule to avoid stockouts between supplier shipment arrivals is the ideal setup for your inventory. While this is easier said than done, it’s highly achievable if you are maintaining a buffer stock with your inventory management system.
Do you find yourself frequently worrying about stocking out while waiting for your shipments to arrive? I’ve been there myself, and the anxiety can indeed be heart-pounding. As an Amazon seller, there are several consequences to stocking out. Aside from the possibility of losing ground on your hard-earned product rankings (which you’ve worked so hard to earn and maintain), the lost revenue from being out of inventory is usually one of the biggest expenses during a stockout. Yet, there is also a long list of snowball effects that might follow, since Amazon heavily penalizes sellers who don’t take extra precautions to keep their inventory levels healthy, especially in recent times.
The good news is that you don’t need to reach this state of despair if you are proactive with your inventory forecasting and keep a sufficient buffer stock in your warehouse. Yes, buffer stock can be a life-saver! And we’ve laid out everything you need to know about it in this article.
In this Buffer Stock vs Safety Stock vs Anticipation Inventory guide, we’ll cover:
Why Is Accurate Forecasting Important?
Inventory forecasting is a technique used to predict the inventory levels needed for a future period by analyzing past data, trends, and known future events. Accurate inventory forecasting ensures businesses have the inventory needed to fulfill future customer orders, which can lead to an increase in revenue and a decrease in unnecessary expenses.
Less On-Hand Inventory
Storing too much inventory in bulk in a warehouse is not usually profitable for your business due to compounding storage fees. With data-based predictions, you’ll only be purchasing the inventory that you’ll need for a given time period plus a little cushioning. (More on that later.) This will improve the inventory accounting as well as increase your funds for other areas of your business.
Fewer Out-Of-Stock Items
By accurate inventory forecasting, your business will have enough products on hand and lowers the risk of a stockout. Having fewer out-of-stock items means more sales since customers won’t be needing to shop elsewhere if you can provide them with what they need and want. Customer experience also remains positive when shoppers find what they’re searching for instead of encountering an “out-of-stock” notice.
More Systematic Production Cycle
Managing your products across the entire supply chain gets a lot better with inventory forecasting. Knowing your manufacturer’s lead times, your warehouse transfer schedule, and the exact stock levels for your products allows you to work more efficiently with your vendors. You can also make better decisions and eliminate the need to rush production schedules and send air shipments by having a better comprehension of production cycles.
Buffer Stock vs Safety Stock vs Anticipation Inventory: The Main Difference
You may have come across these terms at a certain point in your business, but what do they really mean? Today, we’re going to deep dive into these topics, and hopefully, you’ll learn some insights that can help you navigate your inventory management systems.
Let’s get into it!
What is Buffer Stock?
Buffer stock inventory is the extra product set aside to compensate for unexpected delays from suppliers or when the demand is greater than anticipated. Buffer stock is always kept on hand when there’s uncertainty in the demand and supply and within your supply chain to ensure that you can provide what your customer is looking for and prevent an out-of-stock situation.
What is a good buffer stock level?
When you’re thinking about your company’s buffer stock, consider the number of products that must be kept within your inventory so you’ll never miss a sale. Your business will be at a loss if you let your inventory run down to zero before your next shipment arrives.
To avoid stockout, your buffer stock level should be high enough to compensate for any delays that could arise. Make sure to keep in mind the total lead time (production time plus shipping time) as a component of calculating for restocking; this transit time is a crucial part of replenishing your inventory. Your reorders should occur as a combination of the inventory that would be needed during that lead time plus that “just-in-case” extra inventory cushion of buffer stock.
The important thing to note is that there are several factors that should go into determining the best buffer stock for your business as well as where to keep your buffer stock.
Consider splitting your buffer stock between Amazon and a third-party warehouse. This is because you may need more backup inventory than Amazon will currently allow you to have due to their restock limits. You don’t want to hold too much inventory at Amazon but you also don’t want to hold too little and here’s why:
Then, there is something called geo-ranking. This is something within the Amazon algorithm that determines where you will rank on the page within a certain geographical area. It can also determine whether your PPC ads will show up in that area or not.
This is because Amazon makes a couple of promises to their customers and none of them have to do with whether your product will be good or not. Amazon’s promises are that they will allow for mostly hassle-free returns or replacements and they offer their Prime customers free 2-day shipping.
Why is this important? Because if you don’t have enough inventory dispersed throughout the country and Amazon doesn’t think it can fulfill an order within that 2-day time frame, they may not want their customers to purchase that product. Thus, they may not let ads show that product within that area. They may push it down the ranking in that area. All this stunts your sales in these areas. Sellers have seen 1-Day Prime Badges even disappear when they have too little inventory in stock.
For this reason, you have a balancing act. You need to not have too much inventory that you run out of space based on restock limits but enough inventory that is well-dispersed so you don’t see the negative effects of geo-ranking.
Due to Amazon’s storage policy change to using restock limits per storage type instead of per ASIN, it has become more important than ever to prioritize your best sellers and use a good buffer stock to make sure you never run out of those products.
Methods for Calculating Buffer Stock
Buffer stock is more effective if you know the amount of stock you need to keep so that you can prevent higher holding costs from having too much stock on hand and on the other side avoid loss of sales from too little stock.
Calculating buffer stock using a formula may help you to figure out the optimal amount of stock you need for your business.
There are several methods for calculating buffer stock. Each method uses different factors, but they all require your lead time — the time between the initiation of an order and the completion of the delivery process.
1. Fixed Buffer Stock
- Fixed buffer stock is a method of calculating buffer stock used by an inventory manager without using a particular formula. They determine the amount of buffer stock needed from the maximum daily usage for over a period of time and unless they decide to change the value for fixed buffer stock, it remains unchanged.
- Fixed buffer stock is a total number of units that you hold for that particular product and doesn’t fluctuate. For example, for a slower seller, you may list 200 units as your fixed safety stock.
2. Time-Based Calculation
- Buffer stock levels in a time-based calculation are calculated over a specific time period based on a data-driven prediction for the product. It is a method for calculating buffer stock that includes a combination of actual demand and forecasted demand. Using it can present the risk that you might end up keeping a large amount of unwanted stock if your products are moving slower than predicted.
- Another way to look at time-based calculations that tends to be more flexible and less risky is to use a set number of total days of inventory that then fluctuates based on the current sales velocity of the product. For example, 30 days of inventory which, in your slow season could be 900 units and during your peak season could be 3000 units. The idea would be for the buffer stock to adjust with your sales demand.
3. The General Formula
- The general formula is the most simple and popular method for calculating buffer stock. It is used for calculating the average buffer stock needed by your business to hold to prevent any potential out-of-stock situation. buffer stock in the general formula is calculated as the product of the maximum daily usage (the maximum number of units sold in 1 day) and the maximum lead time (the longest time it has taken your supplier to ship the stock) subtracted by the product of average daily usage (the average number of units sold in 1 day) and average lead time (the average time taken by the supplier to deliver the stock).
Buffer Stock = (max. Daily usage)(Max. Lead Time) – (Ave. Daily Usage)(Ave. Lead Time)
As a general rule of thumb for most private label sellers, 30 days of buffer at Amazon, at least for your top sellers, is a good buffer stock.
Advantages of Having Buffer Stock
The main reason for utilizing buffer stock in your business is to avoid out-of-stock scenarios. Stockouts have a negative impact on your business obviously; not only do they represent direct sales and revenue loss, but they also affect your Inventory Performance Index Score as well as your restock limits.
What is Safety Stock?
Safety stock is simply another term for buffer stock, and there’s really no difference between them in terms of meaning.
Key Parameters for a Safety Stock
Some of the key parameters for setting your safety stock quantities are:
- Having accurate predictions concerning demand and supply, which can help estimate volumes.
- Knowing the replenishment frequency required for transferring stock from your 3PL.
- Factoring supplier lead times for production and shipping.
- Product perishability in terms of the shelf lives of the goods.
- Seasonal changes also need to be considered by keeping safety stock.
What is Anticipation Inventory?
Anticipation inventory is the stock that is usually kept seasonally to meet a forecasted increase in demand. Businesses should store inventory on hand in anticipation of events that will or might occur.
One example of anticipation inventory can be sellers in the clothing niche — knowing that summer is approaching, they may acquire enough shorts, skirts, swimsuits, and many more items for an expected spike in demand due to a change in season.
To fully develop your anticipation inventory, you may want to look at a calendar of holidays to be sure you are not missing key events and sales opportunities such as Mother’s Day, Father’s Day, Back to School, and Memorial Day. Prime Day and Black Friday, of course, would be major events for anticipation inventory.
Advantages and Risks Related to Anticipation Inventory
The main advantage of anticipation inventory is that it allows sellers to serve the consumers consistently based on seasonal buying patterns.
There are major risks that go with using anticipation inventory, including:
- Wrong predictions lead to under or overestimations of inventory with a consequence of possible loss of sales or a longer time for the company to sell through it.
- Anticipation inventory gives more carrying costs in which the company will have to spend more money on additional storage fees.
- If the inventory is for a particular season or sales holiday, such as Memorial Day, it at times needs to be sold with a discount or at a lower price.
Buffer Stock Tips And More for Accurate Inventory Forecasting
There are three main “fixes” that SoStocked uses to fix inventory problems so that you accurately forecast the correct amount and order at the right time. They are:
1. Removing sales spikes.
- You may have had Lightning Deals recently that caused your sales velocity to increase significantly. This sudden sales increase interferes with your predicted inventory forecast, which will have a snowball effect on the accuracy of your next order date. It’s essential to remove these sales spikes to eliminate the possibility of over-ordering.
2. Removing stockouts.
- This is the exact opposite of what we mentioned above regarding sales spikes. Stockouts can cause under-ordering if not removed on your forecast calculations. For example, if you stocked out 10 days of the last 30 days while using the last 30 days to forecast your projected sales for the next month, you are potentially going to under-order and stock out before your next order arrives.
- It is critical to determine the right average sales you should base your forecasting on without these stockouts to order the right amount of inventory next time around.
- Removing outliers such as sales spikes and stockouts is what we call Adjusted Velocity. Ideally, you are eliminating the abrupt rises and falls in your sales velocity to give you a realistic image of what your future sales will be if everything goes to plan.
3. Applying Buffer Stock
- Buffer stock makes all the difference in your inventory management. Acting as the false zero alerts that trigger you to make an order when you’ve reached your buffer stock critical level, it allows you to continue with your selling operations while your next order is on its way to your warehouse. Think of it like the Empty light on your car when you’re running low on gas that immediately warns you to go to the nearest gas station.
- Again, as mentioned above, while buffer stock can be expressed in the number of days or units, calculating it based on the number of days using adjusted velocity will give you a better projection as to when you should replenish your inventory.
Action Items
I feel you. Inventory management can be very overwhelming, but we are here to help. Here are some suggestions that you might want to consider.
- If you’re wondering where you should go from here, I suggest that you attend my free live webinar to learn more about inventory management pro tips. By investing 1 hour of your time, you can learn valuable insights on how to streamline your inventory, ALL FOR FREE!
- Ideally, you should sign up for an Amazon inventory management software such as SoStocked.com to automate your systems.
- But if you think this isn’t the right time yet to use inventory management software for your business, you should grab our free Amazon FBA Inventory Spreadsheet Template as a guide.
Need more information?
- Send Message: We typically reply within 2 hours during office hours.
- Schedule Demo: Dive deeper into the nuances of our software with Chelsea.
- Join Live Upcoming Webinar: New to Amazon inventory management? Learn three inventory techniques you can implement right away.